To make cement slurry, mix cement and water in a 1:1.5 ratio until smooth. Ensure the mixture is lump-free for best results.
Cement slurry is essential in construction projects for its binding properties. It seals gaps, adheres materials, and reinforces structures effectively. Ideal for both small repairs and large-scale applications, cement slurry enhances durability. Properly mixing cement and water ensures a consistent, workable paste.
This blend can fill voids, coat surfaces, and stabilize foundations. Builders rely on its versatility and strength. Quality slurry prevents cracks and improves structural integrity. Always measure ingredients accurately for optimal performance. Using cement slurry can significantly improve project outcomes. This simple yet powerful mixture is a staple in construction and repair work.

Credit: m.youtube.com
Introduction To Cement Slurry
Cement slurry is a simple but essential mixture used in construction. It consists of cement, water, and sometimes additives. This combination creates a smooth, fluid paste that can be easily applied. Understanding how to make cement slurry is crucial for many building projects.
The Basics Of Cement
Cement is a binding material used in construction. It is a key component in concrete and mortar. Cement is made from limestone, clay, and other materials. These ingredients are heated in a kiln to form a hard substance called clinker. The clinker is then ground into a fine powder, which we know as cement.
There are different types of cement, including Portland cement, which is the most common. Each type of cement has unique properties. Portland cement, for example, is known for its strength and durability. Knowing the type of cement you need is important for your project.
Importance Of Slurry Consistency
The consistency of the cement slurry is very important. It affects the strength and durability of the final structure. A well-mixed slurry ensures that the cement particles are evenly distributed. This creates a uniform and strong bond.
To achieve the right consistency, you need to measure your ingredients carefully. Use the correct ratio of cement to water. Typically, a 1:1 ratio is a good starting point. You can adjust the amount of water to get the desired consistency.
Ingredient | Amount |
---|---|
Cement | 1 part |
Water | 1 part |
Mix the cement and water thoroughly until you get a smooth paste. Use a mixing tool or a drill with a mixing attachment. Avoid lumps and dry spots in your mixture. The slurry should be fluid but not too watery.
- Uniform mixture: Ensures even distribution of particles.
- Proper bonding: Leads to a strong and durable structure.
- Easy application: Makes the slurry easy to spread and work with.
By maintaining the right consistency, you can ensure the success of your construction project. A well-mixed cement slurry leads to a strong and durable structure.

Credit: www.angellematerials.com
Materials Required
Creating a perfect cement slurry requires the right materials. You need specific cement types, water, additives, and the right tools for mixing. This section covers everything you need to make an effective cement slurry.
Cement Types
Different projects need different cement types. Here are some common types:
- Portland Cement: The most common type, ideal for general use.
- White Cement: Used for decorative work and surfaces.
- Rapid Hardening Cement: Perfect for quick-setting needs.
- Low Heat Cement: Suitable for large-scale concrete projects.
Choose the right cement type based on your project requirements.
Water And Additives
Water is essential for making cement slurry. Use clean, potable water for the best results. The amount of water affects the slurry’s consistency.
Additives can improve the slurry’s performance. Here are some common additives:
Additive | Purpose |
---|---|
Plasticizers | Increase workability |
Retarders | Delay setting time |
Accelerators | Speed up setting time |
Choose the right additives to match your project’s needs.
Tools For Mixing
Using the right tools is crucial for making cement slurry. Here are the tools you’ll need:
- Mixing Bucket: A large, sturdy bucket for mixing.
- Mixing Paddle: Attach to a drill for efficient mixing.
- Measuring Tools: Accurate measuring cups or containers.
- Protective Gear: Gloves, goggles, and a mask for safety.
Gather all tools before starting to ensure a smooth process.
Safety First
Before starting any construction project, it’s crucial to prioritize safety. Making cement slurry is no exception. Understanding and implementing safety measures can prevent accidents and ensure a smooth workflow. Let’s dive into the essential safety practices you need to follow.
Personal Protective Equipment
Wearing the right Personal Protective Equipment (PPE) is vital. Here’s a list of the necessary gear:
- Safety goggles to protect your eyes from dust and debris.
- Gloves to shield your hands from corrosive materials.
- Dust mask to prevent inhalation of harmful particles.
- Long-sleeved clothing to protect your skin.
- Steel-toed boots to safeguard your feet from heavy objects.
Safe Handling Of Materials
Safe handling of materials is another crucial aspect. Follow these steps to ensure safety:
- Store materials in a dry, cool place to prevent moisture absorption.
- Lift bags of cement correctly to avoid back injuries. Bend your knees and keep your back straight.
- Mix materials in well-ventilated areas to avoid inhaling dust.
- Use clean tools to avoid contamination of the slurry.
- Dispose of waste materials properly to prevent environmental harm.
By adhering to these safety guidelines, you can ensure a safe and efficient cement slurry preparation process. Always remember, safety should be your top priority.
Preparation Steps
Making cement slurry involves several crucial steps. Each step ensures the mixture is smooth and effective. Follow these guidelines for the best results.
Measuring Ingredients
Accurate measurement is key to a good cement slurry. Use a measuring bucket for this step.
- Water: Use clean water. Measure the water needed for the batch.
- Cement: Use a high-quality cement. Measure the required amount.
- Additives: If using additives, measure them accurately.
Below is a simple table to help with measurements:
Ingredient | Measurement |
---|---|
Water | 4 liters |
Cement | 10 kg |
Additives | As required |
Preparing The Workspace
Having a clean and organized workspace is essential.
- Clear the Area: Remove any debris or obstacles.
- Gather Tools: Ensure all tools are within reach. This includes buckets, mixers, and trowels.
- Protective Gear: Wear gloves and goggles to protect yourself.
Preparing the workspace ensures a smooth process and prevents accidents.
Mixing The Perfect Slurry
Creating the perfect cement slurry requires precision and attention to detail. Whether you are a professional builder or a DIY enthusiast, understanding the right mixing process can ensure a strong and durable result. Below, we will explore the step-by-step process to achieve the ideal slurry consistency, and address common issues you might face during mixing.
Step-by-step Mixing Process
- Gather your materials: You will need cement, water, a mixing bucket, and a mixing tool.
- Measure your ingredients: For a standard slurry, use a 2:1 ratio of water to cement.
- Add water first: Pour the measured water into the mixing bucket.
- Add cement gradually: Slowly add the cement to the water while stirring continuously.
- Mix thoroughly: Use a mixing tool to combine the ingredients until you achieve a smooth, lump-free consistency.
- Check consistency: The slurry should be thick but pourable, similar to pancake batter.
- Adjust as needed: If too thick, add small amounts of water. If too thin, add more cement.
Troubleshooting Common Issues
Even with careful preparation, issues can arise. Here are solutions to common problems:
Issue | Solution |
---|---|
Lumpy slurry | Mix more thoroughly or use a whisk attachment on a drill. |
Too thick | Add water in small increments and mix until the right consistency. |
Too thin | Gradually add more cement while mixing to thicken. |
Slurry setting too fast | Use cool water and mix in a shaded area to slow down the setting time. |
Slurry not setting | Ensure a proper cement-to-water ratio and check the cement’s expiration date. |
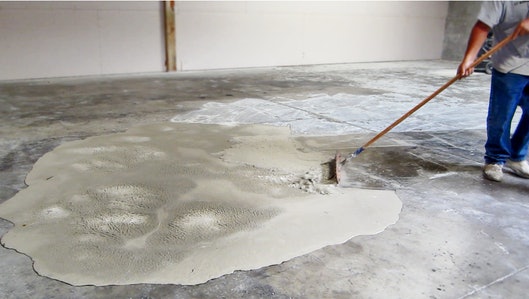
Credit: www.forconstructionpros.com
Application Techniques
Understanding the application techniques for cement slurry is crucial for achieving durable and smooth surfaces. Whether you’re laying foundations or filling gaps and holes, each method has its own set of best practices.
Laying Foundations
For laying foundations, follow these steps:
- Prepare the area by removing any debris and leveling the ground.
- Mix the cement slurry to a smooth consistency.
- Pour the slurry into the foundation mold.
- Use a trowel to spread the slurry evenly.
- Allow it to set for at least 24 hours before proceeding.
Ensure the foundation mold is well-sealed to prevent slurry leakage.
Filling Gaps And Holes
Filling gaps and holes effectively requires attention to detail:
- Clean the area thoroughly to remove loose particles.
- Mix the cement slurry to a thick but pourable consistency.
- Use a putty knife to fill the gaps and holes with the slurry.
- Press the slurry firmly to ensure it fills all spaces.
- Allow it to set and dry completely before painting or sealing.
Filling gaps and holes with cement slurry can prevent structural damage and improve appearance.
Drying And Curing
Understanding the drying and curing process is crucial for making cement slurry. These steps ensure that the cement achieves its full strength and durability. Proper drying and curing prevent cracks and structural failures. Let’s dive into the optimal conditions and timeframes for these processes.
Optimal Conditions For Curing
Curing cement slurry requires maintaining moisture, temperature, and time. The ideal temperature range is 50°F to 90°F. If the temperature is too low, curing will be slow. High temperatures can cause rapid drying, leading to cracks.
Keep the cement surface moist. You can use water sprays, wet burlap, or plastic sheets. This moisture is essential for the chemical reactions in the cement. These reactions give the cement its strength.
Protection from wind and direct sunlight is also necessary. Wind and sun can cause the cement to dry too quickly. This rapid drying can lead to weaker cement with cracks.
Timeframes For Drying
The initial drying period for cement slurry is 24 to 48 hours. During this time, the surface will become firm. Avoid any heavy loads or traffic on the surface.
Complete curing can take 7 to 28 days. For optimal results, keep the cement moist throughout this period. Here is a simple timeframe guide:
Time Period | Process |
---|---|
24-48 hours | Initial drying, surface firms up. |
7 days | Partial curing, cement gains initial strength. |
28 days | Full curing, cement reaches maximum strength. |
Remember to maintain the optimal conditions throughout the drying and curing periods. This attention to detail ensures the cement slurry will be strong and durable.
Cleanup And Maintenance
After making cement slurry, it’s crucial to clean up properly and maintain your tools and materials. This ensures the longevity of your equipment and the quality of future mixes.
Cleaning Tools
Cleaning your tools right after use prevents cement from hardening on them. Hardened cement can damage tools and make them unusable.
Here’s a simple cleaning process:
- Rinse Immediately: Rinse all tools with water right after use.
- Scrub Thoroughly: Use a stiff brush to scrub off any remaining cement.
- Soak if Needed: Soak tools in water if cement has started to harden.
For best results, use a wire brush for stubborn spots. Always wear gloves to protect your hands.
Storing Unused Cement
Proper storage of unused cement is essential to maintain its quality for future use.
Here are some tips for storing unused cement:
- Keep It Dry: Store cement in a dry place to prevent moisture absorption.
- Seal Tightly: Use airtight containers or bags to keep moisture out.
- Elevate Storage: Store cement off the ground to avoid dampness.
Using these methods will ensure your cement remains effective for the next project. Proper maintenance saves time and money.
Advanced Tips
For those looking to achieve the perfect cement slurry, these advanced tips will help. By focusing on customizing mix ratios and enhancing slurry performance, you can ensure a superior finish.
Customizing Mix Ratios
Customizing mix ratios is crucial for achieving the desired consistency and strength. Here are some steps to follow:
- Understand the basics: The standard mix ratio is 1 part cement to 2 parts sand.
- Adjust for specific needs: For a stronger mix, use a 1:1 ratio. For a smoother finish, add more water.
- Test small batches: Before committing, test small batches to find the right consistency.
Consider using a digital scale for precise measurements. This ensures consistency across different batches. Additionally, keep a record of your mix ratios and results. This helps replicate successful mixtures in future projects.
Mix Ratio | Application |
---|---|
1:2 | General use |
1:1 | High-strength applications |
1:3 | Smoother finishes |
Enhancing Slurry Performance
To enhance the performance of your cement slurry, consider the following tips:
- Use additives: Additives can improve workability, strength, and curing times.
- Maintain proper water ratio: Too much water weakens the mix. Use just enough to achieve the desired consistency.
- Mix thoroughly: Ensure all components are well-blended to avoid weak spots.
Some common additives include plasticizers and silica fume. Plasticizers improve flow without adding extra water. Silica fume enhances strength and durability. Always follow manufacturer guidelines when adding these to your mix.
Proper curing is also essential. Keep the slurry moist during the curing process to prevent cracks and ensure a strong finish. Cover the surface with a damp cloth or plastic sheeting to retain moisture.
By following these advanced tips, you can create a high-quality cement slurry that meets your specific needs and enhances the overall performance of your construction projects.
Can I Use Cement Slurry for Plastering?
Yes, you can use cement slurry for plastering. It helps to fill in the gaps and cracks in the wall and provides a smooth surface for painting. When choosing the best cement for plastering, make sure to consider the quality and durability of the product for a long-lasting finish.
Frequently Asked Questions
How Is Cement Slurry Made?
Cement slurry is made by mixing cement, water, and sometimes additives. The mixture forms a fluid paste used in construction.
How Do You Make A Cement Slurry Mix?
To make a cement slurry mix, combine cement and water in a 1:1. 5 ratio. Stir until smooth. Adjust water for desired consistency. Use immediately.
What Is The Ratio Of Cement Slurry?
The typical ratio for cement slurry is 1:1, meaning equal parts water and cement. This ratio ensures proper consistency and strength. Adjustments might be needed based on specific project requirements.
What Is A Cement Slurry?
Cement slurry is a mixture of cement, water, and additives. It is used in construction for sealing and binding. This mixture helps in the solidification of structures and prevents fluid migration.
Conclusion
Mastering the art of making cement slurry can enhance your construction projects. With the right mix, achieving perfect consistency is simple. Follow these steps to ensure durability and strength. Cement slurry is a versatile component in many building applications. Start your next project with confidence and precision by understanding this essential process.
{ “@context”: “https://schema.org”, “@type”: “FAQPage”, “mainEntity”: [ { “@type”: “Question”, “name”: “How is cement slurry made?”, “acceptedAnswer”: { “@type”: “Answer”, “text”: “Cement slurry is made by mixing cement, water, and sometimes additives. The mixture forms a fluid paste used in construction.” } } , { “@type”: “Question”, “name”: “How do you make a cement slurry mix?”, “acceptedAnswer”: { “@type”: “Answer”, “text”: “To make a cement slurry mix, combine cement and water in a 1:1.5 ratio. Stir until smooth. Adjust water for desired consistency. Use immediately.” } } , { “@type”: “Question”, “name”: “What is the ratio of cement slurry?”, “acceptedAnswer”: { “@type”: “Answer”, “text”: “The typical ratio for cement slurry is 1:1, meaning equal parts water and cement. This ratio ensures proper consistency and strength. Adjustments might be needed based on specific project requirements.” } } , { “@type”: “Question”, “name”: “What is a cement slurry?”, “acceptedAnswer”: { “@type”: “Answer”, “text”: “Cement slurry is a mixture of cement, water, and additives. It is used in construction for sealing and binding. This mixture helps in the solidification of structures and prevents fluid migration.” } } ] }